
(ガントリーローダ)
NCオートローダ
工場の製造ラインで工作物を自動搬送する装置です。
稼動の信頼性を誇る卓越した搬送技術をご評価いただいています。
メンテナンスサービスも行っており、故障の無い安定した生産に貢献しています。
LNⅣ-30(搬送対象物:自動車エンジン部品・クランクシャフト)
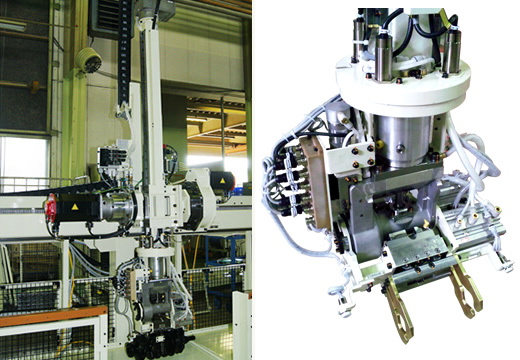
クランクシャフト、カムシャフトなどの軸物工作物用。
1アーム2ハンド旋回方式を採用。
< 特徴 >
1. 高速・高精度で工作物の着脱を実施
2. クランプつめを1本にすることで段取り替えレスに対応
水平旋回軸の搭載で姿勢変換装置が不要
項目 | 仕様 | 備考 |
---|---|---|
工作物搬送重量 | 30 ㎏ |
30㎏×2個の搬送では 最大級機能を保有 |
キャリア走行速度 | 200m/min | |
アーム上下速度 | 120m/min | |
アームストローク | Max1200㎜ | |
爪旋回 | 135 度 | |
水平旋回 | 270 度 | 姿勢変換装置不要 |
把持部 | 1 本爪 | 無段取り替え対応を実現 |
LNⅣ-5(搬送対象物:自動車エンジン部品・カムシャフト)
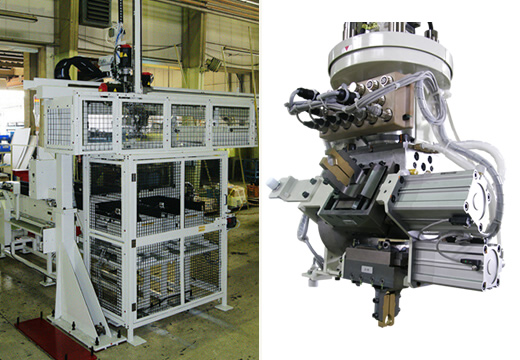
項目 | 仕様 | 備考 |
---|---|---|
工作物搬送重量 | 5 ㎏ |
5㎏×2個の搬送では 最大級機能を保有 |
キャリア走行速度 | 200m/min | |
アーム上下速度 | 120m/min | |
アームストローク | Max1200 ㎜ | |
爪旋回 | 135 度 | |
水平旋回 | 270 度 | 姿勢変換装置不要 |
把持部 | 1 本爪 | 無段取り替え対応を実現 |
New Model (5kgローダ)
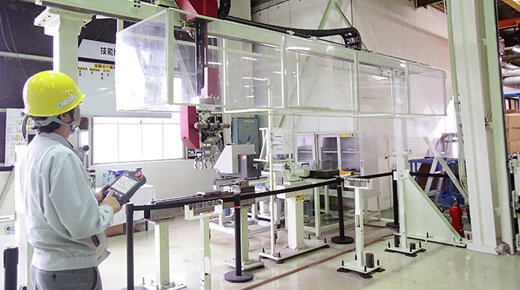
スリム・シンプル・ハイスピード240m/minを実現
・タブレットでの簡単なティーチング操作が可能
・低コストで高機能
LN-15T(搬送対象物:エンジン部品・シリンダーヘッド・ブロック)
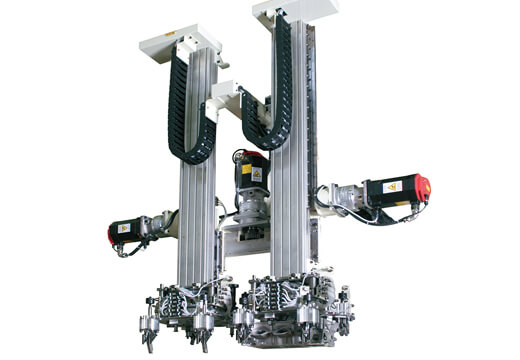
シリンダヘッド、シリンダブロックなどの箱物工作物用。
2アームタンデム方式を採用。
< 特徴 >
フローティング機構によるM/C治具へのダイレクト挿入を実現
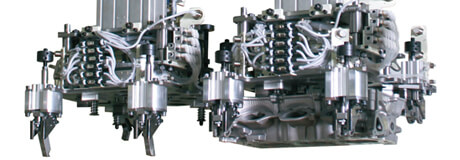
多くの実績と信頼
ローダは止まると該当ライン全てが止まってしまいます。
そのため当社の機械装置は、稼働の信頼性=長時間故障がなく正常に稼働する点を重視しています。
信頼性第一の設計思想が「壊れにくい」機械装置のご提供につながっております。
万全なアフターサービス
突発的な故障にも迅速に対応しております。ご安心ください。
また、ローダ・転造盤のいずれについても、立ち上げには現地での調整が必要となります。
当社ではそれらの作業にもしっかり対応していきます。

完全自社製で一貫生産
機械設計・制御設計・製作施工まで一貫して実施します。
事業の歴史も古く、お客様の高い要求水準に対応する技術力についてもご評価いただいております。
これらの考え方や取組みに基づき、よりお客様のお役に立つ機械装置の開発を目指しています。
お気軽にご相談ください。
※お問い合わせは、お電話 または ホームページお問い合わせからご連絡ください。
(転造盤)
NC転造盤
切りくずを出さない塑性加工マシンで、環境負荷の低減に貢献しています。
本体構成が一体型の鋳物ですので非常に精度良く加工することが可能です。
シャフト転造
転造例
TZ120-140×630
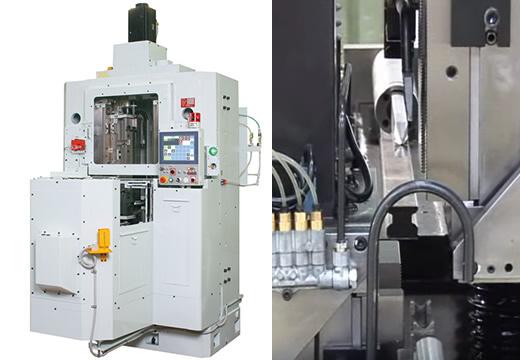
高荷重な転造に対応。
一体型コラムにより高剛性を実現。
< 特徴 >
1. 安定した高精度な加工
2. 高い生産性
3. 切りくずを出さず、材料をムダにしない(環境負荷低減)
TZN6-80
中荷重の転造に対応。
OPD調整作業を自動化し、安定した高精度を実現。
地上での段取り替え作業が可能。
< 特徴 >
サーボモーターによるOPDの自動調整機能を搭載
段取り替え作業の容易化を実現
安定した高精度
- OPD (Over Pin Diameter) 調整作業を自動化 -
段取革新
- 刃具交換の容易化 -
機械仕様
転造係数 Coefficient of Max. Rolling | 80 |
最大転造部径(mm) Max. Rolled Portion | Φ50 |
最大転造モジュール(mm) Max. Rolling Module | 1.3 |
刃具台取付スペース(mm) Tool Post Setting Space | 250 |
刃具移動ストローク(mm) Tool Travel Stroke | 700 |
最大刃具長さ(mm) Max. Tool Length | 630 |
電源 Power Source | AC200V 50/60HZ |
機械質量(kg) Machine Mass | 7,000 |

工事環境改善製品リサイクル・CO2削減への限りなき挑戦・工場環境改善のお手伝いをさせて頂きます。
工場環境の改善をサポートします。
クーラントシステム
高清浄度ろ過システムで加工機の性能維持やランニングコストの低減に貢献します。
加工機を人に例えると、クーラント装置は血液をろ過する腎臓といえます。
クーラントをきれいにすることで加工機の生命を支えています。
加工機に合わせて、様々なバリエーションをご用意しています。
高精度部品研削用クーラントシステム K100,K200(5ppm仕様)
・高精度な部品(油圧ロッドやスピンドルなど)の研削用にデザインされたシステム
・従来システムで残留したスラッジを90%削減(80ppm→5ppm)!!
*1ppm=1mg/Lの残留スラッジ量
<特徴>
1. 2段ろ過により清浄度がさらに安定
2. ろ過装置に高精度マグネットセパレータとサイクロンを搭載
3. フィルタレスで環境負荷低減
4. システムの小型化によって、省スペース化を実現(従来比60%削減)
<効果>
1. ドレスインターバルが延長し、砥石の寿命向上
2. 切りくず噛み込みによる真円度不良を解消し、研磨キズ(シューマーク)の発生を改善
3. 清浄度の向上によって更液周期が延び、ランニングコストが低減
高精度ろ過クーラントシステム Dシリーズ(30ppm仕様)
・量産部品(自動車部品など)の研削用にデザインされたシステム
・高精度マグネットセパレータとサイクロンを搭載し、従来システムで残留したスラッジを60%以上削減(当社比)
<特徴>
1. 長期に渡って清浄度30ppmを維持し、加工機の清掃周期を延長
2. 機器のシンプル化によって、省スペース(15%減)・省エネ(19%減)を実現
<効果>
1. 切りくずの噛み込みによる加工不良を解消
2. ランニングコストの低減が可能
二重円形クーラントシステム「タマラン」
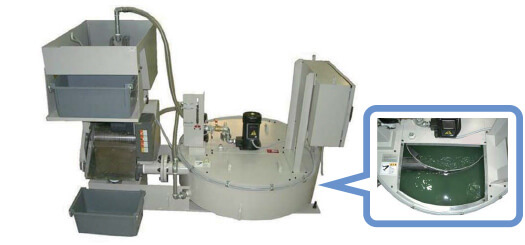
研削液のロングライフ化を目指してタンクを四角から円形に発想転換。タンク内のスラッジ堆積を解消した二重円形クーラントシステムです。清浄度の安定、省スペース、低価格を実現。
タマランは、高清浄度・省スペース・低価格の円形クーラントシステムです。
(マグネットセパレータ)
高性能マグネットセパレータ MXシリーズ
高清浄度ろ過システムで加工機の性能維持やランニングコストの低減に貢献します。
・業界最高磁力(最遠部の磁力:当社調べ)
・取り逃がさない磁場設計のもと、捕集率が大幅に向上(従来比2倍以上)。
今まで捕集できなかった弱磁性体(SUJ2など)も確実にキャッチ。
<特徴>
1. 最適磁石配列により流路全域を高磁束密度化
2. ドラムに浸硫窒化処理を実施し、キズが付きにくく脱水性を維持
3. ドラム駆動部がクーラントと接触しない構造のため、高寿命
4. 従来のME/MFシリーズと互換性のある構造で、置き換えが簡単 油性クーラントにも対応
クーラントシステム組立工場
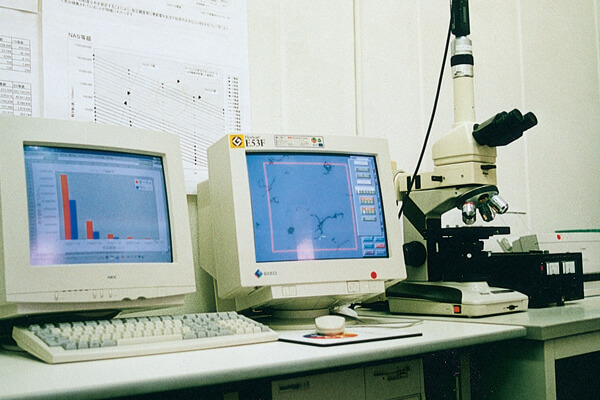
モニタリング実施中
1. 加工不良や設備故障でお困りのお客様を対象に、クーラント液診断を実施しています。
2. 高性能マグネットセパレータ(MXシリーズ)をお客様の工場で、一定期間お試しで使用していただき、その前後でクーラント液を分析評価し、改善点を見つけます。
サイクロン濾過装置
(研削切粉圧縮機)
パーフェクトRECシステム
金属研磨スラッジリサイクル技術
研削屑の硬化処理による再利用を実現しました。
油水分離機・オイルスキマ
環境対策必需品 40年の実績
浮上油をすばやく回収します。
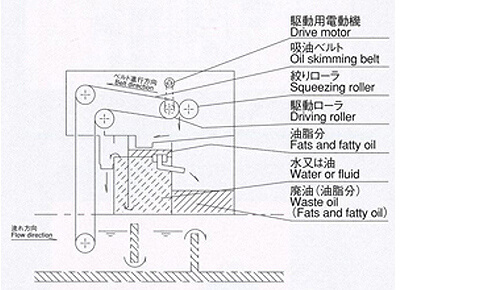
顕微鏡試料作製機
環境対策必需品 40年の実績
浮上油をすばやく回収します。
マイクロカット 試料切断機
マイクロプレス 試料成型機
マイクロラップ 試料手動研磨機
マイクロサーフェイス 試料平面修正機